High Efficiency Electro-Hydraulics
The Scorpion 350 takes its hydraulic power from the Power Beyond ports of the tractor. The load-sensing system ensures maximum efficiency and does not require any cooler.
Large diameter hoses reduce the energy losses. All the functions of the harvester are grouped together in a hydraulic manifold with cartridge valves. The modular design is economical and easy to maintain.
The hydraulic functions provide precision and power. The connection is easy thanks to color and symbol coded anodized aluminum handles. Only 4 lines are required for all functions. |
Hydraulic Feedroll Drive
A heavy-duty, 46cc piston motor, coupled with a robust transfer box provide high output torque to feed the impressive harvester capacity. The simple setup largely reduces the number of parts.
The use of a hydraulic motor brings the benefits of smooth starts, independent of the PTO speed. The slow reverse speed ensures precise control of the feedrolls when reversing after a metal detection for example. |
Easy to use ISOBUS Controls
Operating a forage harvester has never been so user-friendly. The Scorpion 350 connects to the ISOBUS implement connector of the tractor to load the graphical interface in the tractor display. For non-ISOBUS tractors, a retrofit kit is available including a connection harness and monitor. The graphical interface provides a complete visualisation of the harvester state, adjusts the length of cut & operation functions.
For an optimal and ergonomic operation, an Aux-N ISOBUS joystick is recommended (available as an option). Some tractors allow the assignation of ISOBUS functions directly on the armrest joystick or button, making it even easier. |
Advanced and Useful Functions
//
Belt Slippage Monitoring
To avoid failure or overload, speed sensors are installed to detect slippage of the different driving belts. An audible and visual alarm will show any critical slippage and the harvester feedrolls and header will automatically stop if it persists or worsens.
//
Overload Protection
With the electronic feedroll speed management, an anti-clogging feature is integrated. In case of a decrease of the PTO speed under a critical threshold, by mistake or due to overload, the feedroll speed will decrease sharply or stop completely to avoid stalling the tractor. You can then maximise the forward speed of the tractor without risks of clogging the cutterhead.
// Live Load Display
Pressure sensors on the feedroll hydraulic motor allow a direct monitoring of the feedroll load. The color coded dynamic graphical display lets you quickly visualize the data to get maximum performance from the harvester.
//
Hour Counter
Allows for the monitoring of controller and cutterhead hours.
// Adjustable Spout Rotation Speed
To get the optimum speed for the situation, the spout rotation can be adjusted to any of the 10 pre-set levels at any moment from the monitor.
//
Automatic Inoculant Mode
The liquid application system can be set to turn ON and OFF automatically according to the feedroll opening. A manual mode is also available |
Renowned quality of cut, ideal length of cut
Available with a Dion cutterhead with 8 or 12 knives depending on your requirement. The helicoidal knives with tapered profile cut precisely with low power requirement.
The hydraulic feedroll drive of the Scorpion 350 allow a high precision on the adjustment of the LOC to obtain the ideal silage sample at any time. The 1mm step adjustment is done directly from the ISOBUS terminal. This system, unique to Dion, also offers the widest LOC range on the market, up to 24mm (0.94in)* with a 12 knife cutterhead. |
Range of Length of Cut – 12 knives (mm) |
Range of Length of Cut – 8 knives (mm) |
Simplified Sharpening & Adjustment
Nothing is more important for good harvester performance and silage quality than the sharpness of the knives and the shearbar adjustment. To make the task easier, the time to execute these tasks has been reduce by 50% compared to the previous models and nothing on the market can compare in terms of simplicity. The forward sharpening on Dion harvesters provides a razor sharp edge while drawing the sharpening heat away from the knife tip and without leaving a burr.
The simplified sequence reduces the sharpening and bar adjustment to two simple steps. Start the PTO, sharpen, and adjust! No driveshaft to disconnect, no repetitive travels between the tractor seat and the harvester. With a rack & pinion system, the shearbar is loosened by two lockers, standing on one side of the harvester. Sliding on integrated ramps, it moves parallel to the cutterhead by a single adjustment bolt. This simple method encourages the operator to maintain proper adjustments and knife sharpness. The reduction in wear, fuel consumption and resulting excellent silage quality will add up to gains in profitability. |
The FerroDtec Precision
The new FerroDtec metal detector from Dion combines precision and reliability. Programmed on powerful controllers, it offers an exceptional reaction time. The new algorithm allows for precise and reliable detections while reducing the risk of time consuming false detections. The detection threshold is automatically calibrated to the condition of the crop and the wear or damage of the detector feedroll. Ten (10) levels of sensitivity, selected manually, allow you to adapt to any requirement.
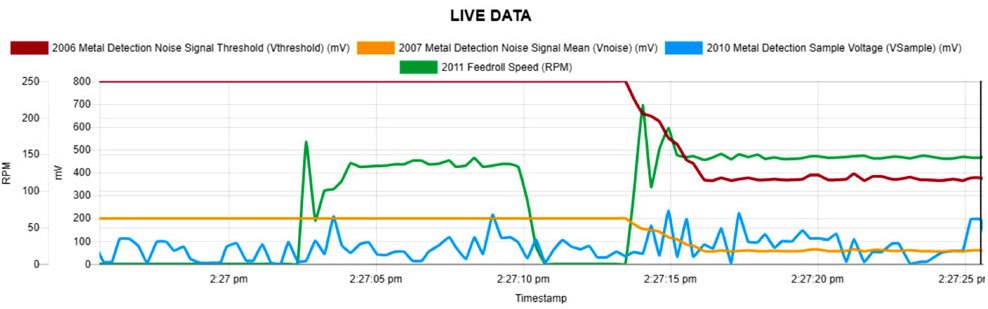
|
High-Tech without Gadget
The benefits of technology should not be a burden to reliability. In case of a sensor failure, the critical electronic functions can be deactivated to operate in a “failsafe” mode to keep harvesting temporarily. Silage quality is the priority.
Your dealer is equipped with a complete service and diagnostic software that allows the technician to analyse the performance of the electronic system. Through the Wi-Fi connection on a laptop computer, the live system data can be displayed, even from the cab while harvesting in the field! A faster and more precise diagnostic results in less repair costs. The harvester control software updates are done quickly and easily and allow you to benefit from eventual system improvements. |
Mechanical Header Drive
The header is driven by a quick coupled driveshaft. Without chain to install, the change of headers is done in a few minutes. The engagement of the header is done through a hydraulically control belt binder with automatic tension control. The reverse operation is powered by a separate hydraulic motor for a smooth engagement and high available torque. The feedrolls and header can be reversed without the PTO engaged. |
The Unique Stinger Spout
With exceptional dimensions, the 2nd generation Stinger spout loads on any side, even the tallest trailers. The accelerator/blower power of the Scorpion allows side-loading to considerably reduce trailer switching time for even more productivity.
// Max height : 5.8m (19ft)
// Rotation : 330 deg
Mounted on a solid base, the Scorpion 300 is “Stinger ready” as a standard feature. A double deflector, also standard, ensures a precise filling in pull-behind trailers as well as for side loading. Even in short configuration, you benefit from an ultra-durable 1/4in thick Hardox wear plate. Accessible directly from the top, it can be replaced in a few minutes.
Reach the next level with the Stinger extension option which can be “dealer or field installed” very quickly. No additional brace or support is required. Also, the transition between the short and long configuration is done in a few minutes: ideal for contractors. Optional for the standard spout configuration, a wireless camera and LED spout light are standard with the Stinger extension. They let you harvest on both sides with ease.
The redesigned dual accumulator suspension provides a smooth ride in Stinger configuration. For road transport, the spout is lowered at a height below 3m (10ft). The suspension absorbs the impacts or road imperfections no matter the speed. When set in transport position, the rotation is automatically locked for safe travels between fields.
|
Shear Processing with τSτ
A proven concept, exclusive to Dion, the optional processor rolls of the Scorpion 350 uses a shearing effect to process the particles and pulverise the kernels in corn silage. With a differential speed ratio of 67%, the highest on the market, the particles are torn lengthwise and the grain is processed with low crushing pressure. This reduces compression forces and improves KP bearing life all while reducing power requirements.
The lower 10” roll is paired with the smaller 6” top roll, both turning at close to 4000rpm. They are positioned directly in the crop flow trajectory to eliminate direction changes and lower energy consumption. Obtain the desired level of silage processing at any time by simply adjusting the clearance of the processor rolls, in a few seconds, with a single wrench.
The conversion time between corn silage configuration and haylage has been reduce by approximately 30% compared with the previous models. The top roll is completely removed by sliding it out towards the inside of the harvester where it can be stored onboard to reduce handling. No major parts need to be removed or displaced. It is done with a single wrench, with less effort and all adjustments are preserved for a quick reinstallation. |
Manufacturing Quality
The desire to provide a durable and modern product was part of the design process of this new generation of harvesters. The rated power of the driveline has been increased. Premium quality, banded belts, have been selected for highest durability and power transmission capacity.
You will notice the superior quality powder coat paint and extensive usage of plating on several parts. We can count on qualified welders and master assemblers to offer a reliable product. |
Practical and Ergonomic
Harvest in style with the new color scheme and completely redesign guards. A large main guard opens with ease to access the drive components. The access is direct to the length of cut chain binder for easy adjustment. The hydraulic module pivots to give access to the service points. "Butterfly” guards protect the core of the harvester and the sharpening system from debris accumulation.
The completely new tongue combines rigidity and accessibility. Cable and hose routing have been improved. Finally, remain visible at any moment with the LED transport lights |